In healthcare, meticulously maintaining medical equipment and managing inventory are critical to clinic operations. The quality of health services relies on functional, reliable equipment which requires regular maintenance. Navigating this process involves understanding the equipment and implementing an efficient inventory management system. The challenge lies in balancing equipment reliability with cost management. This discussion focuses on creating cost-effective maintenance schedules and inventory strategies, enhancing healthcare delivery quality.
Understanding Equipment Maintenance
Equipment maintenance comprises regular inspections, cleaning, repairs, and replacements for optimal performance and longevity. Regular upkeep mitigates unexpected breakdowns and costly downtime, extending equipment lifespan. Maintenance training is essential, enabling personnel to identify issues, perform routine tasks, and understand when professional help is needed. This training standardizes maintenance practices, boosting efficiency.
The maintenance frequency depends on equipment usage, environment, and manufacturer guidelines. Schedules should consider peak usage and operational periods to limit operational disruption. Documentation is key in maintenance, providing records of activities, issues, resolutions, and aiding in future planning, troubleshooting, and cost-effective replacement decisions.
The Importance of Maintenance Schedules
Maintenance schedules are crucial in equipment management, serving to prevent breakdowns and boost clinic efficiency. Their meticulous planning and strict adherence can extend equipment life, reduce downtime, and improve operational productivity.
Preventing Equipment Breakdown
Regular equipment maintenance is crucial for preventing breakdowns and enhancing operational efficiency. Breakdown predictors are key to determine maintenance frequency and intensity. Consider these points:
- Inspections: Identify potential issues to prevent breakdowns.
- Predictive analysis: Use data to pinpoint possible failure points, enabling proactive measures.
- Maintenance prioritization: Focus on key clinic equipment to reduce downtime.
- Training: Equip staff with skills in equipment operation and basic troubleshooting.
Enhancing Clinic Efficiency
A robust maintenance schedule, underpinned by regular inspections, predictive analysis, and staff training, is pivotal in enhancing clinic efficiency. It optimizes equipment functionality, mitigates downtime, and circumvents unexpected equipment failures, enabling timely replacements or repairs. Staff competency in implementing maintenance schedules, identifying potential issues, and executing minor repairs is critical. This operational efficiency not only facilitates smooth clinic functioning but also boosts patient satisfaction by ensuring prompt and effective healthcare delivery. Thus, a comprehensive maintenance schedule is essential for optimized clinic performance and patient satisfaction.
Types of Equipment in Clinics
In clinical healthcare, diverse equipment types, including diagnostic, therapeutic, life support and patient monitoring equipment, are vital. Their lifespans and upgrade trends are essential for inventory management and healthcare services efficiency.
- Diagnostic Equipment: Tools like X-ray machines, ultrasound devices, MRI scanners, and blood testing apparatus are included. Lifespan depends on use frequency and technology type.
- Therapeutic Equipment: This includes infusion pumps, laser systems, and physical therapy devices. Technological advancements lead to frequent upgrades, reducing their lifespan.
- Life Support Equipment: Critical tools for patient survival like ventilators, dialysis machines, and defibrillators. Due to robust construction and high replacement costs, these have a longer lifespan.
- Patient Monitoring Equipment: Heart rate, blood pressure, and respiratory monitors are part of this category. Frequent upgrades are common due to rapid medical technology evolution.
Optimized management of these equipment categories ensures high-quality patient care delivery in clinics.
Inventory Management: An Overview
Inventory management is vital for equipment longevity and efficient operation. It significantly influences facility productivity through inventory control. Implementing effective strategies ensures smooth equipment operation.
Understanding Inventory Management
Effective inventory management, essential for a business’s resource optimization, involves the meticulous control of component ordering, storage, and use in production. This process, however, faces inventory challenges that can disrupt stock accuracy.
- Inaccurate Forecasting: Disturbs supply-demand equilibrium by causing overstock or stockouts.
- Poor Record Keeping: Generates disparities between actual stock and logged data.
- Inefficient Storage: Wastes space, incurring unwarranted expenses.
- Lack of Regular Audits: Permits unnoticed errors to accumulate over time.
These factors highlight the need for rigorous, detail-focused inventory management to ensure efficient resource usage and smooth business operations.
Importance of Inventory Control
Inventory control is essential for a company’s profitability and performance. It involves ensuring inventory accuracy, which helps reduce costs related to excess stock and stockouts, and boosts customer satisfaction. It aids in making informed decisions about replenishment strategies, product lifecycle management, and capacity planning. Stock optimization, another key element, maintains a balance between demand and supply, reducing overstock and understock risks. This enhances operational efficiency and contributes to a company’s financial stability and growth.
Effective Inventory Strategies
Understanding and applying effective inventory strategies is key for optimal business operations and profitability enhancement.
- Inventory Categorization: Prioritize resources by segmenting inventory based on value, usage, and demand. High-value inventory receives more attention.
- Supplier Relationships: Secure timely essential inventory delivery by fostering strong supplier relationships.
- Demand Forecasting: Prevent overstock or stock-out by predicting future demand using historical data and market trends.
- Regular Audits: Maintain inventory accuracy, identify discrepancies, and rectify them promptly through routine checks.
Proper implementation of these strategies leads to improved inventory control, cost reduction, and increased profitability.
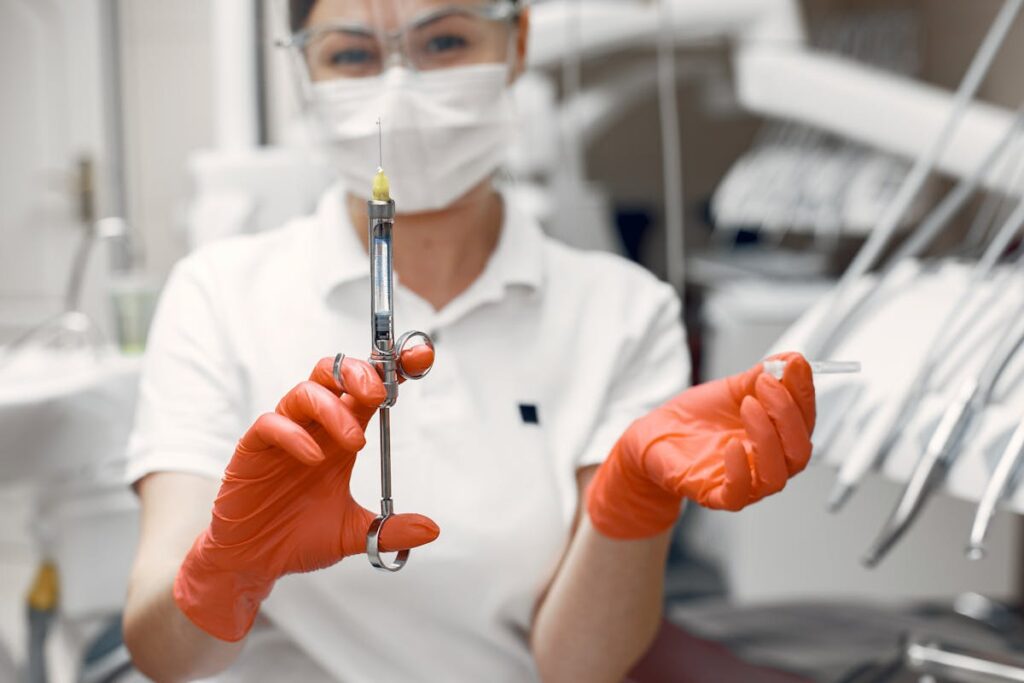
Steps to Develop Maintenance Schedules
Creating a maintenance schedule involves planning, data recording, and understanding equipment needs. The focus is on schedule optimization to reduce disruption and extend equipment lifespan, requiring deep knowledge of each equipment piece, usage patterns, and wear susceptibility.
Maintenance flexibility, the capacity to adjust the schedule based on sudden changes like equipment breakdowns or usage pattern shifts, is crucial. To accommodate unexpected events, a ‘buffer time’ should be incorporated into the schedule.
The first step is compiling an equipment inventory, including make, model, purchase date, and current condition. This information predicts potential maintenance needs and schedules them to minimize disruption.
The next step is setting maintenance task frequency, based on manufacturer recommendations, past maintenance records, and equipment criticality. The process is periodically repeated to keep the schedule up-to-date and relevant.
Implementing Maintenance Schedules
Implementing maintenance schedules is vital for equipment management, optimizing efficiency and minimizing downtime while prolonging equipment longevity. The process involves creating effective timetables and understanding their significance. This text discusses the design steps and potential implementation challenges. Each word and sentence is optimized for natural language processing (NLP) and semantic search engines, ensuring clarity and context.
Importance of Schedules
Adhering to a precise equipment maintenance schedule is crucial for optimal machine performance and longevity, enhancing productivity and operational efficiency. Specifically, in a clinical setting, it offers several benefits:
- Routine inspection enables early problem detection, reducing equipment failure and repair costs.
- Regular upkeep extends equipment’s service life, maximizing return on investment.
- Well-maintained machinery operates efficiently, conserving energy and resources.
- It minimizes work-related accident risks, ensuring staff and patient safety.
Designing Effective Schedules
Creating a meticulous and uniform maintenance schedule is crucial for optimal equipment performance. Efficient scheduling software aids in this process, ensuring no important maintenance tasks are missed.
Preventive measures, including regular inspections, cleaning, adjustments, and replacements, are the core of these schedules. These actions prolong equipment lifespan and reduce expensive breakdowns. When designing schedules, consider equipment type, usage frequency, and importance to clinic operations. This comprehensive approach produces a practical and efficient maintenance schedule, enhancing overall clinic productivity.
Challenges in Implementation
Implementing maintenance schedules faces challenges such as adherence, resource allocation, technical complexities, and change management.
- Adherence: Consistent follow-through on schedules is challenging. Automated reminders can aid in adherence.
- Resource Allocation: Limited resources necessitate careful planning and efficiency.
- Technical Complexities: Maintenance requires understanding equipment’s technical aspects, necessitating specialized knowledge.
- Change Management: Staff resistance can delay or hinder new system implementations.
Proactive planning and problem-solving effectively manage these challenges.
Maintenance Schedule Challenges
Effective equipment maintenance scheduling poses challenges such as resource allocation, timeline adherence, and minimal operational disruption. Unplanned downtime, a major unpredictable hurdle, impacts clinic productivity and disrupts schedules by requiring immediate resources. Vendor relationships can expedite securing parts or services, but over-dependence can risk control loss and cost escalation.
The maintenance schedule should balance flexibility for equipment failure unpredictability and rigidity for regular preventative maintenance. This balance necessitates detailed planning, resource management, and proactive communication. Overcoming these challenges involves a structured approach focused on preventative measures, contingency planning, and strong vendor relationships. With proper planning, challenges are mitigated, ensuring smooth operations and extended equipment life in clinics.
Technological Tools for Maintenance
Utilizing innovative tech tools enhances maintenance efficiency, mitigates equipment upkeep challenges in clinical settings. Tools like Digital Diagnostics, Predictive Analytics transform maintenance scheduling through real-time, accurate insights on equipment performance and potential issues.
- Digital Diagnostics: Enables real-time equipment condition monitoring, identifies potential issues, reduces downtime, and prolongs clinical equipment lifespan.
- Predictive Analytics: Uses machine learning, artificial intelligence to predict potential failures based on historical data, current conditions, facilitates preemptive maintenance.
- Internet of Things (IoT): IoT devices monitor, report equipment usage, conditions, provide data for efficient inventory, maintenance management.
- Cloud-based Maintenance Management Software: Provides centralized maintenance records, schedules, inventory status storage, promotes maintenance team coordination, enhances process transparency.
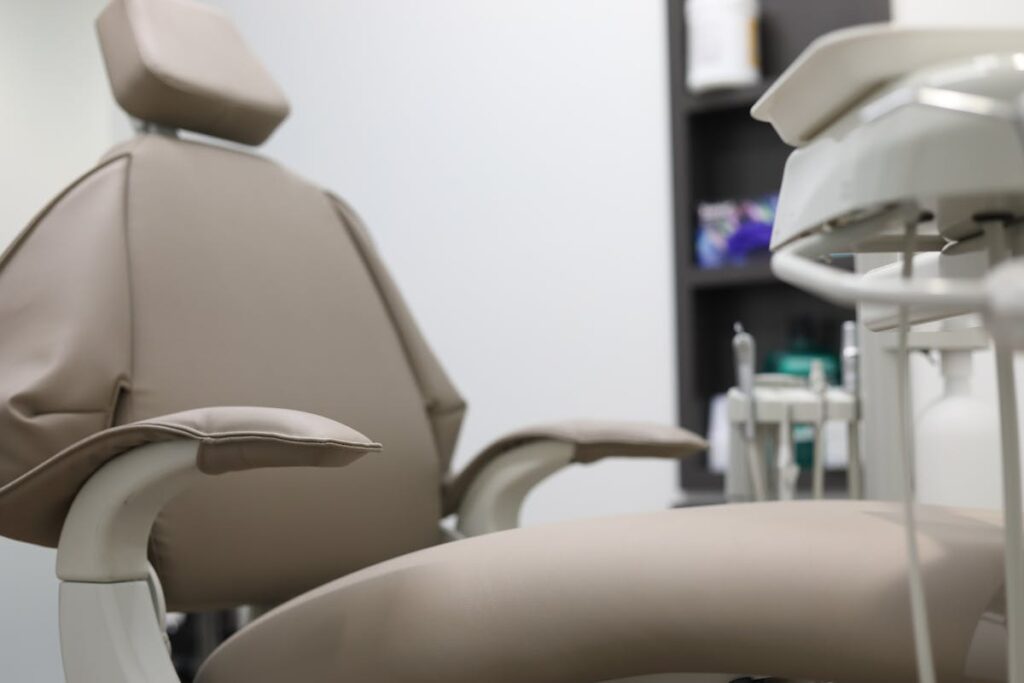
Regular Check-Ups Vs Major Repairs
In equipment maintenance, regular check-ups and major repairs are key to optimal performance and longevity. Regular check-ups, acting as preventive measures, reduce equipment failure risk, unexpected repair expense, and unforeseen downtime.
A strict schedule for routine inspections aids early detection of minor issues, preventing their escalation into major problems. This approach enhances equipment functionality, extends service life, and lowers the necessity for expensive and lengthy major repairs.
Despite this, some situations necessitate major repairs. These high-cost repairs can revive equipment efficiency, eliminating the need for total replacement. The impact of such repairs on operational downtime must be carefully planned to minimize clinical disruption.
The cost-effectiveness and practicality of regular check-ups versus major repairs hinge on various factors like equipment age, usage frequency, and budget constraints. Achieving the right balance requires continuous monitoring and reassessment.
Cost-saving Benefits of Maintenance
Regular equipment maintenance yields cost-saving benefits. These include:
- Downtime Reduction: Regular checks prevent equipment failure, reducing unproductive downtime, enhancing productivity and profitability.
- Extended Equipment Lifespan: Routine maintenance prolongs equipment life, avoiding premature replacements and reducing capital expenditure.
- Efficient Resource Utilization: Preventing major repairs enables strategic resource allocation for critical processes, maximizing operational efficiency.
- Cost Analysis: Maintained equipment inventory facilitates accurate cost analysis, optimizing budget allocation, and eliminating unnecessary costs.
Case Study: Successful Maintenance Plans
In this real-world case, a Chicago healthcare facility significantly boosted equipment efficiency and lifespan, and cut operational costs, by implementing a successful maintenance plan. This plan involved proactive equipment upkeep through a robust maintenance software, enabling regular device checks to ensure optimal condition.
The software’s implementation resulted in fewer unexpected repairs due to early detection and rectification of potential problems. This strategy minimized equipment downtime, thus, ensuring continual device availability for patient care. Over time, this approach extended equipment lifespan and led to considerable cost savings.
Furthermore, the software provided critical data analytics, allowing for maintenance schedule adjustments based on equipment usage and performance trends. This precision added to the management’s maintenance planning.
This case study underscores the significance of systematic, technology-aided maintenance in clinics. It shows how such a plan enhances equipment performance, extends its lifespan, and reduces costs, particularly those tied to unexpected repairs. It highlights the worth of investing in advanced maintenance strategies.
Future Trends in Equipment Maintenance
Analyzing the case study, we identify four key trends in equipment maintenance shaping the future of healthcare operations.
- Predictive Maintenance: This trend leverages machine learning and artificial intelligence for early detection of potential equipment problems. The outcome is reduced downtime and enhanced patient care quality.
- IoT Integration: IoT devices capture and transmit real-time equipment data, enabling immediate maintenance notifications and failure alerts. Analysis of this data optimizes maintenance schedules, prolongs equipment life and cuts costs.
- Augmented Reality (AR): AR supports maintenance by offering technicians interactive, virtual instructions. This reduces errors and boosts efficiency.
- Automation: Automated systems streamline maintenance task scheduling, tracking, and implementation, enhancing efficiency, accuracy, and regulatory compliance.
Predictive maintenance and IoT integration, among these trends, will transform equipment maintenance in healthcare facilities. Proactive adoption ensures optimal equipment functionality, improving patient care and outcomes.
Frequently Asked Questions
What Kind of Training Is Required for Staff to Properly Operate and Maintain Clinic Equipment?
Staff require training in equipment operation, preventive maintenance, and troubleshooting for effective use and longevity of clinic equipment, contributing to improved patient care and operations.
Are There Any Legal or Regulatory Requirements Related to Equipment Maintenance in Clinics?
Indeed, clinics must adhere to legal and regulatory stipulations concerning equipment maintenance. Compliance demands systematic record-keeping of maintenance activities, verifying equipment safety for patient use.
How Does Equipment Maintenance Impact Patient Safety and Satisfaction in Clinics?
Patient safety and satisfaction in clinics hinge on equipment maintenance. Regular upkeep lessens costs, boosts equipment longevity, ensures peak performance, minimizes downtime, and enriches care quality. Thus, maintenance impacts patient safety and satisfaction directly.
Can the Same Maintenance Schedules Be Used for Different Types of Equipment in a Clinic?
Different clinic equipment types require unique maintenance schedules due to varying lifespans and costs. This approach ensures optimal performance, extends equipment life, and boosts patient safety and satisfaction.
Is There a Role for Patients in the Maintenance and Upkeep of Clinic Equipment, Such as Home-Use Medical Devices?
Patient participation in home-use medical device maintenance is essential. It fosters correct usage, prolongs equipment life, and guarantees maximum efficiency, thereby enhancing health management and patient recuperation.