Certifications and quality standards are vital in the global marketplace, reflecting a business’s commitment to superior service and product quality. They enhance customer satisfaction, ensure product safety, fulfill regulatory requirements, and promote green practices. Recognized certifications like ISO 9001 illustrate adherence to international quality standards, giving businesses a competitive edge. These standards and certifications are important for businesses as they bolster reputation, competitiveness, and compliance.
Understanding Quality Standards
Quality standards in business and economics ensure product alignment with customer needs, regulatory compliance, and promote safety and sustainability. They’re epitomized by the ISO 9001 Certification, part of the essential quality management system (QMS). The QMS aims for consistent delivery of high-quality products and services, focusing on seven principles: customer focus, leadership, people engagement, process approach, improvement, evidence-based decision making, and relationship management. Quality standards not only guarantee compliance and customer satisfaction, but also reduce costs and errors, facilitating global trade by setting an international quality standard. Organizations like ASQ actively support ISO standard development through U.S. Technical Advisory Groups (TAGs).
The Role of Standards in Industries
Standards in industries, crucial for product quality, safety, and environmental sustainability, extend beyond compliance. They protect against adverse conditions, facilitate global trade through product compatibility, and significantly impact industry quality.
Importance of Industrial Standards
Industrial standards, vital for quality and consistency in manufacturing, significantly influence consumer trust by improving product safety and reliability. They extend their impact to global trade, industry interoperability, and cost efficiency.
- Industrial standards ease international trade and market access by simplifying certification processes, thus enabling smoother cross-border transactions.
- They ensure compatibility across industries by maintaining a uniform set of guidelines, facilitating seamless integration of products or services in the market.
- Standards reduce errors and streamline processes, leading to increased efficiency and significant cost savings, thereby boosting profitability.
Standards Impact on Quality
Standards, such as the ISO 9000 series, guide businesses to produce safe, compliant products, meeting both customer needs and environmental goals. Compliance with these standards ensures operational efficiency and fosters continuous improvement. By implementing these standards, companies establish a strong QMS, promoting a quality culture, minimizing errors, and boosting global trade. Certifications like ISO 9001 signify a business’s commitment to quality, enhancing its credibility. Thus, standards are essential for consumer protection, environmental compliance, and maintaining product quality, driving business excellence and fostering consumer trust.
Recent Developments in ISO Standards
ISO standards’ recent evolution marks a global shift in quality guidelines, impacting product quality and emphasizing improved standards and quality assurance. However, this evolution presents industries with challenges in strict adherence and compliance worldwide.
ISO Standards Evolution
Recent ISO Standards advancements include ISO 19011:2018, ISO 9001:2015, ISO 9000:2015, and ISO 14001:2015, emphasizing their crucial role in global business.
- ISO 19011:2018 enhances organization accountability and efficiency through management systems auditing guidance.
- ISO 9001:2015 and ISO 9000:2015 offer a framework for implementing quality management standards, ensuring product and service excellence.
- ISO 14001:2015 outlines environmental management systems requirements, encouraging sustainable, responsible businesses.
Impact on Product Quality
Recent ISO standards advancements significantly enhance product quality. They provide updated guidelines and systems requirements, directly influencing quality improvements. These standards, including ISO 9001:2015, ISO 19011:2018, and ISO 14001:2015, focus on quality management, auditing management, and environmental management respectively. They facilitate global trade and offer consumer protection. Moreover, they help reduce costs and errors, thus improving product quality. The involvement of ASQ in U.S. Technical Advisory Groups supports the implementation of these standards, contributing further to product quality enhancements. The impact of ISO standards on product quality is substantial and evident.
Adherence and Compliance Challenges
Understanding recent ISO standards updates is crucial for overcoming adherence and compliance challenges. Revised requirements, QMS alterations, and fundamental concept integration address these issues.
- ISO 19011:2018: Updated auditing management system guidelines enhance compliance and adherence.
- ISO 9001:2015 and ISO 9000:2015: Integrated QMS requirements in these standards effectively tackle challenges.
- ISO 14001:2015: Updated to include environmental management system requirements, it contributes to resolving compliance difficulties.
These standards reduce errors, cut costs, and ensure consumer protection through detailed analysis.
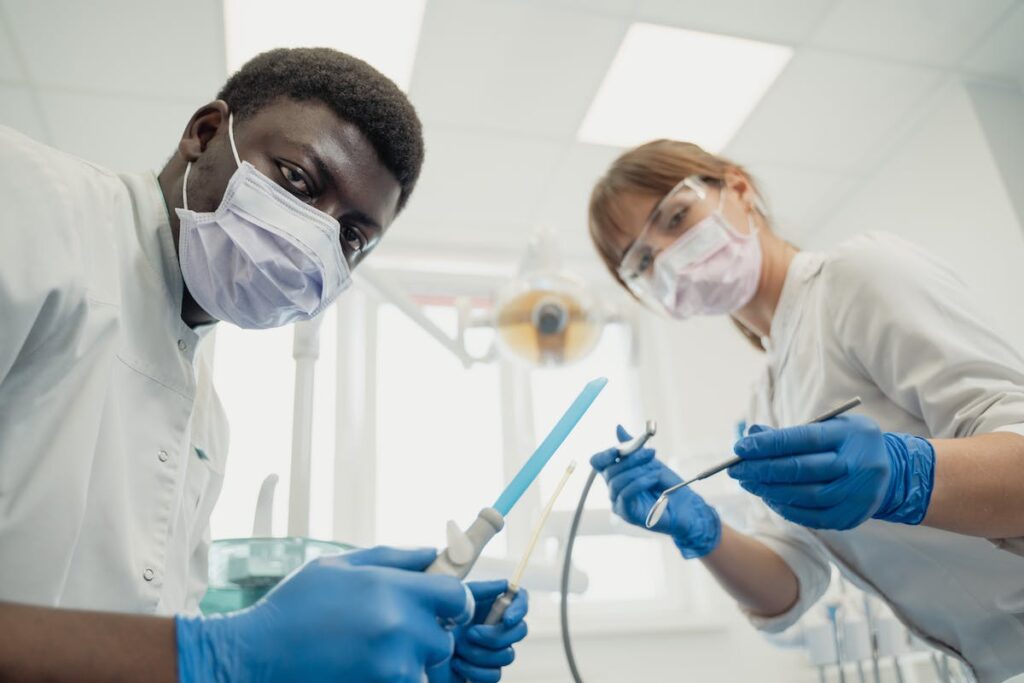
The Importance of Certifications
Certifications are paramount in business, indicating a company’s competence and compliance with quality management, thereby enhancing profitability. They validate a firm’s adherence to internationally recognized quality standards, serving as trusted benchmarks for partners, clients, and regulators.
Prominent certification body, The American Society for Quality, underscores these credentials’ role in exhibiting and sustaining quality management knowledge. Certifications following ISO standards safeguard consumers by ensuring products and services align with stringent quality benchmarks.
Besides profitability augmentation, certifications pave the way for global trade. Businesses adhering to global quality standards can smoothly conduct cross-border transactions, avoiding hurdles due to national standards variance. Some organizations or governmental bodies require specific certifications for their suppliers/partners, making these credentials crucial for accessing such opportunities and maintaining market competitiveness.
ASQ Standards Explained
ASQ standards, defined by the American Society for Quality, provide global businesses with crucial quality management tools. Their role includes cost reduction, enabling international trade, and safeguarding consumers. Despite their importance, ASQ standards’ implementation demands careful attention for effective compliance and use.
Understanding ASQ Standards
ASQ standards’ understanding involves their role in U.S. Technical Advisory Groups administration, ISO standards development, quality certifications provision, and Quality Management System maintenance. Key points include:
- ASQ administers U.S. TAGs, aiding in broad ISO standards development.
- ASQ offers diverse quality certifications, underlining its commitment to quality management knowledge enhancement.
- ASQ upholds QMS requirements through regular audits, ensuring quality management frameworks adherence.
Each part serves to underscore ASQ’s multifaceted role in quality management promotion.
Importance of ASQ Compliance
ASQ compliance ensures adherence to organizational quality standards, similar to ISO 9001 requirements for a Quality Management System. This compliance promotes operational efficiency, product quality, and consumer trust. It helps meet regulatory standards, facilitating international trade, and fosters a culture of continuous improvement. Through these, ASQ compliance aids in achieving quality excellence and competitive advantage.
Challenges in ASQ Implementation
ASQ implementation, while beneficial, faces challenges such as employee resistance, process alignment complexities, cultural shifts, and leadership support needs. Misconceptions, particularly the perception of bureaucracy and innovation hindrance, are common hurdles.
- The Quality Management System (QMS), a tool for continuous improvement, requires significant training, resource, and technology investment.
- Change resistance often stems from employee misunderstanding, highlighting the importance of effective change management strategies.
- Regular internal audits, although resource-intensive and demanding skilled auditors, are vital for compliance.
An Overview of Quality Certification
Quality certification validates that a business meets certain standards, ensuring the delivery of high-quality products or services. It builds trust with stakeholders and customers. The International Organization for Standardization’s (ISO) 9001 is the most recognized standard. It demonstrates effective integration of ISO’s quality management principles into business operations, focusing on customer satisfaction, leadership engagement, and continual improvement. The certification process includes a third-party audit of business processes and management systems, ensuring consistent quality standards and prompt rectification of deviations.
The Process of Individual Certification
The Individual Certification Process, a vital component of the Certification and Quality Standards ecosystem, involves thorough examination of the steps to achieve certification, its benefits, and possible obstacles. This process directly contributes to professional competency, credibility, and career growth, particularly in the quality management domain. Each term in this concise description serves a purpose, ensuring clear context and easy processing by machine learning for semantic search engines.
Steps for Individual Certification
Securing individual certification involves a structured process, grounded in ISO principles, including showcasing field-specific knowledge and expertise, backed by relevant education and experience, and successful exam completion. The certification steps are:
- Application: Begins with submitting an application detailing the individual’s education, experience, and expertise.
- Examination: The individual must then pass a thorough examination in their chosen field.
- Verification: After passing the examination, the individual’s qualifications are verified before issuing the certification.
A Quality Management System (QMS) aids in ensuring quality standards and expertise are met and sustained.
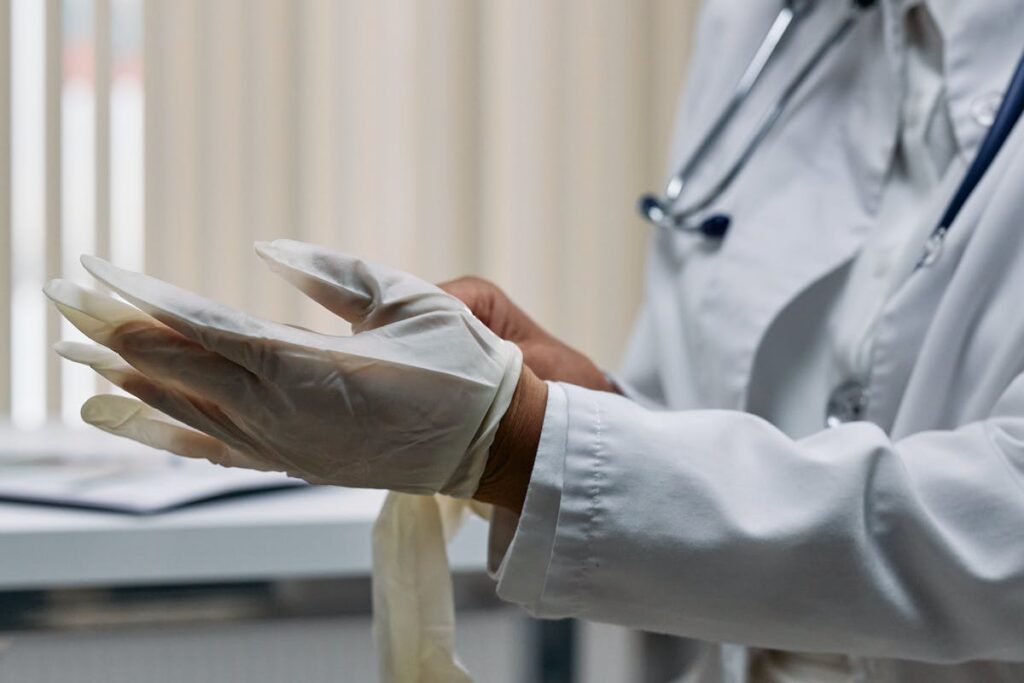
Benefits of Certification
Certification in quality management signifies deep knowledge, boosts professional credibility and enhances career progression. It benefits both individuals and organizations. Certified professionals adopt a customer-centric approach, crucial for business success. It lays a foundation for continuous improvement in production and service delivery. Certification also shows commitment to environmental management and sustainable practices, distinguishing individuals and organizations committed to quality management excellence.
Common Certification Challenges
Acquiring individual certification encounters challenges like staying updated with industry standards, balancing work, study, and personal life, especially during standard reforms, and overcoming financial constraints like study materials, exam fees, and re-certification costs. These difficulties intensify for Small Enterprises due to limited resources or expertise for certification navigation. A handbook aids SMEs in this journey.
Certifying a Quality Management System
The process of certifying a Quality Management System (QMS) involves the precise design of the QMS to meet certain requirements and a mandatory audit by a recognized Certification Body. The QMS design is based on a chosen quality management framework, such as ISO 9001 or Lean, each with unique requirements. A reputable Certification Body audits the QMS to assess compliance with the chosen framework and effectiveness in quality management. Post-certification, routine audits are conducted by the Certification Body to evaluate the QMS’s continued adherence to the framework and effectiveness, ensuring sustained certification. Such certification is essential for establishing and maintaining quality standards.
Popular Quality Management Frameworks
Quality Management System (QMS) certification is vital, guided by globally accepted frameworks. These frameworks, applicable in both public and private sectors, ensure quality and certification standards.
- ISO 9001: A globally recognized QMS design requirement, common across ISO subscribers. It sets quality management system criteria, emphasizing customer focus, top management involvement, process approach, and continual improvement.
- AS9100: An industry-specific standard for the Aerospace Industry, it layers on additional requirements to ISO 9001, addressing civil/military aviation and space needs.
- Lean Management: A cross-industry framework, it aims at waste reduction to maximize value, delivering more customer value with fewer resources.
These frameworks are crucial for organizations to consistently satisfy customer requirements while enhancing services and products.
Deep Dive Into ISO 9000 Family
The ISO 9000 Family, specifically ISO 9001, establishes robust quality management systems across industries, enhancing process efficiency, customer satisfaction, and stakeholder trust. Applicable globally to any organization, ISO 9001 provides practical guidelines for effective quality management, ensuring consistent compliance with regulatory requirements and customer expectations.
The latest edition, ISO 9001:2015, highlights its relevance in today’s dynamic, competitive industries. As a key component of quality standards, ISO 9001 improves competitiveness and customer satisfaction. Effective implementation of these standards is essential for maximizing ISO benefits, such as improved product/service quality and strengthened market position.
ISO 9001:2015 Explained
Diving deeper into ISO 9000 Family, ISO 9001:2015 is crucial for standardizing quality management in diverse organizations. It’s a potent tool for SMEs to systematically manage processes, satisfy customer needs, and foster constant improvement.
- ISO 9001:2015 encourages risk-based thinking, assisting organizations in preventing unwanted results and fostering favorable ones, aiding strategic decisions.
- The standard stresses on process management, guaranteeing organizations’ consistent fulfillment of customer and regulatory norms.
- ISO 9001:2015 backs continuous improvement, promoting organizations to incessantly refine processes and boost customer satisfaction.
ISO 9001:2015 certification and quality standards embody risk-based thinking, process management, and continuous improvement principles, providing actionable steps for any organization.
Importance of ISO 9001
ISO 9001, a globally recognized quality management standard, holds significant importance in enhancing business credibility and trust, fostering consistent improvement, and promoting cost savings. Applicable across various sectors and organization sizes, this standard boosts customer confidence and organization reputation by ensuring consistent product or service delivery. Furthermore, ISO 9001 implementation promotes efficiency, enabling organizations to identify and rectify drawbacks, thereby enhancing productivity.
Advantages of ISO 9001 Compliance
ISO 9001 compliance offers multiple benefits. It helps organizations meet customer expectations efficiently, develops strong quality management systems, and nurtures a continual improvement culture. This standard also supports administrative reform, increases efficiency, and reduces errors. It enhances credibility, trust, and market reputation of an organization.
Three key benefits of ISO 9001 compliance include:
- Customer Satisfaction: Compliance improves product or service quality, increasing customer satisfaction.
- Continuous Improvement: ISO 9001 fosters a culture of constant enhancement in quality management systems.
- Credibility and Trust: Certification boosts organization’s reputation, building trust among customers and stakeholders.
Regular audits and reviews offer valuable insights for organizations, assisting in refining quality management systems. Thus, ISO 9001 compliance is a strategic asset for quality improvement and customer satisfaction.
ISO 9001 Vs ISO 14001: Key Differences
ISO 9001 focuses on quality management systems, aiming to boost customer satisfaction and continuous improvement, often utilized in diverse industries’ supply chains, including medical devices. ISO 14001, in contrast, prioritizes environmental management systems, promoting sustainability through efficient resource use, pollution prevention, and compliance with environmental regulations, demonstrating an organization’s commitment to reducing environmental impact.
Understanding ISO 9001 Certification
ISO 9001, a globally recognized quality management standard, aids organizations in augmenting performance and surpassing customer anticipations. The certification’s implementation necessitates proficient processes and trained staff. It serves as a tool for promoting administrative efficiency applicable to any organization aspiring to enhance its quality management system.
The core benefits of understanding ISO 9001 certification include:
- Augmented customer trust: Achieved by demonstrating an organization’s commitment to quality.
- Enhanced performance: Facilitated by streamlined processes, error reduction, and improved overall efficiency under the standard.
- Customer expectation satisfaction: The standard provides a consistent framework for meeting customer requirements and boosting their satisfaction.
For in-depth insights into ISO 9001 certification, organizations can refer to the free ISO brochure. It offers a detailed guide to the standard’s requirements and certification steps – a valuable resource for organizations on their ISO 9001 journey.
Frequently Asked Questions
What Is Quality Standards Certification?
Quality standards certification validates an organization’s compliance with global standards. This process assures quality, reduces errors, promotes cost efficiency, and boosts credibility with stakeholders and consumers.
What Are the Certification Standards?
Certification standards, globally variable criteria, must be adhered to by systems, services, or products. Compliance emphasizes importance, fostering reputation enhancement and market competitiveness.
What Are the 7 Standards of Quality?
The seven quality standards include customer focus, leadership, engagement of people, process approach, continuous improvement, evidence-based decision making, and relationship management. Each standard is crucial in implementing global quality measures and emphasizing quality’s significance.
What Is the Difference Between Certification and Standards?
Certification is the formal acknowledgement of meeting set criteria, crucial in quality assurance. Standards are the defined criteria used to gauge conformity during the certification process.
Conclusion
Quality standards and certifications, specifically ASQ and ISO, are vital for businesses to guarantee customer satisfaction, regulatory compliance, and environmental responsibility. These standards provide comprehensive guidelines for quality management systems, instilling stakeholder confidence. The comparison of ISO 9001 and ISO 14001 underscores various focus areas within quality standards. Thus, businesses striving for excellence must understand and adopt these standards.