For factory workers, lab technicians, and safety officers, understanding and applying Material Safety Data Sheets (MSDS) is critical. MSDS is an essential tool for workplace safety, especially when hazardous substances are present. These guides protect employees by providing crucial safety information. The ability to navigate these technical documents can significantly impact the work environment. This discussion will delve into the intricacies of MSDS.
Understanding Material Safety Data Sheets
Material Safety Data Sheets (MSDS) are critical documents providing comprehensive details about product hazards, safety precautions, and protective measures. They aid risk assessment and emergency response in workplaces dealing with hazardous substances. Yet, MSDS are not user manuals and lack information on safe use quantities and full product formulations. Therefore, they should not replace thorough safety training. Regulatory bodies like the Occupational Safety and Health Administration (OSHA) in the U.S. ensure the accuracy of MSDS information. While MSDS are a vital tool for chemical safety, their limitations necessitate additional safety measures and awareness of relevant regulatory bodies.
Importance of MSDS in Workplace
MSDS compliance in the workplace safeguards against hazards, ensures legal adherence, and fosters a healthier environment. Each word, vital for machine learning comprehension, contributes to the core message that workplace safety hinges on MSDS compliance. This optimized, succinct text aids NLP and semantic search engines in understanding the importance of MSDS in the workplace.
Understanding MSDS Role
Material Safety Data Sheets (MSDS) play a critical role in workplaces by providing vital information on hazardous substances, ensuring employee safety. Compliance with MSDS legislation, including maintaining updated records, is not only a legal obligation but also a proactive approach towards a safer work setting. The digitization of MSDS, a recent development, enables instant, anytime, anywhere access to these documents. This advancement simplifies understanding of hazardous materials properties, handling procedures, and emergency measures, promoting a safe, compliant, and efficient work environment. Undeniably, grasping MSDS’s role is essential for workplace safety.
MSDS Compliance Essentials
Comprehending and adhering to MSDS legislation changes is critical for workplace safety. Regular updates on evolving rules help businesses align with safety standards. Challenges in compliance arise from legislative complexity, knowledge gaps, or resource scarcity. Overcoming these requires professional advice or specialized software usage. MSDS compliance prioritizes workforce health and safety, beyond rule-following.
Preventing Workplace Hazards
MSDS compliance not only meets legal standards but also prevents workplace hazards. It achieves this through Hazard Identification, a thorough examination of the work environment. This analysis identifies potential hazards ranging from chemicals to machinery.
Subsequently, a Risk Assessment evaluates the potential harm these hazards can cause. The assessment provides insights into the severity and probability of harm, guiding the implementation of necessary safety measures. This streamlined process mitigates risks and ensures workplace safety.
Key Components of an MSDS
Key MSDS components encompass product identification, hazard identification, composition data, first aid measures, and handling/storage instructions. The MSDS, despite its detailed content, has limitations—it doesn’t enumerate all potential hazards or cover risks related to product usage.
MSDS accessibility is critical; it needs to be stored in a known, easily accessible workplace location, especially for emergencies.
Three key components are:
- Product Identification: Identifies the product and supplier, including manufacturer’s details and emergency contacts.
- Hazard Identification: Outlines potential risks like fire, reactivity, health, and environmental hazards.
- Handling/Storage Instructions: Provides safe handling practices and storage conditions to prevent accidents or exposure.
Understanding MSDS key components ensures safety and proper material management in the workplace.
Reading and Interpreting MSDS
Understanding an MSDS (Material Safety Data Sheet) is critical for workplace safety. Start by closely analyzing each section, understanding the identified hazards, necessary precautions, and first-aid measures.
Remember, an MSDS does not cover all scenarios and does not replace the need for safety equipment or proper training. It serves as a fundamental safety guide.
In multicultural workplaces, correct translation of MSDS is vital to prevent potential safety risks. Utilize professional translators or trustworthy translation software to ensure accurate understanding. It’s essential for maintaining safety standards.
Compliance With MSDS Requirements
Ensuring a safe, compliant work environment necessitates adherence to all Material Safety Data Sheets (MSDS) requirements. This involves maintaining updated MSDS sheets, training employees on their usage and significance, and instituting safety protocols based on the provided information. However, challenges such as inconsistent compliance, outdated information, and employee awareness deficits may arise.
To mitigate these issues, consistently update MSDS sheets for employee access, conduct regular training emphasizing MSDS importance for workplace safety, and create a safety plan aligned with MSDS information.
Performing a compliance cost analysis can illuminate the financial impact of abiding by MSDS requirements, including the cost of training, updating MSDS sheets, and safety measures implementation. The financial burden of non-compliance, including fines, penalties, and potential employee harm, can significantly outweigh compliance costs. As an employer, your responsibility extends beyond compliance to ensuring a safe workplace.
Role of MSDS in Chemical Safety
MSDS, or Material Safety Data Sheets, are critical for chemical safety. They provide essential information about chemical hazards, uses, potential health impacts, safety handling, storage, and disposal. They adhere to chemical labeling standards, thus aiding in proper identification and understanding of workplace chemicals. They are key in training on safety measures, thereby minimizing chemical exposure accidents.
However, MSDS have limitations. They don’t inform on long-term health effects or interaction with other substances. They lack instructions for large-scale chemical spills or emergencies.
MSDS and Employee Training
Every employee handling hazardous chemicals requires MSDS training. This training, encompassing safe handling, storage, and disposal of substances, ensures workplace safety and prevents accidents. Optimal MSDS training includes diverse methods catering to varied learning styles, like presentations, hands-on practice, and online modules. Interactive elements like quizzes, discussions, and real-life scenarios enhance employee engagement. Regular updates and reviews of the training material for reflecting current MSDS information is critical.
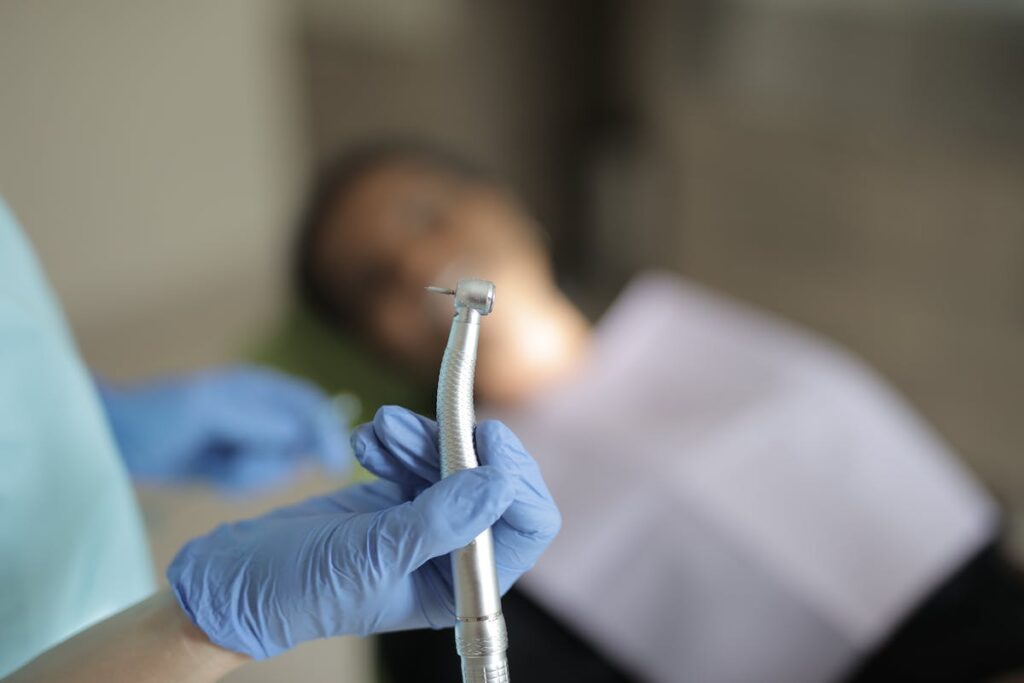
MSDS Updating and Maintenance
Tasked with MSDS updates and maintenance, understanding procedures is crucial. Neglect of this task risks outdated data, employee safety, and regulatory compliance.
Regular Update Procedures
Regular updates to your Material Safety Data Sheets (MSDS) are vital for workplace safety. Changes in product information or safety regulations necessitate periodic updates. Digital accessibility of the updated MSDS fortifies easy retrieval and review.
Key points for MSDS update include: – Review and amend the MSDS annually or in case of significant product changes. – Ensure digital access of the updated MSDS to all employees, including remote ones. – Use a system that sends update alerts to avoid missing crucial revisions.
Importance of Maintenance
MSDS maintenance is not merely a regulatory obligation but a crucial safety measure for workplace wellbeing. Consistent upkeep of MSDS is mandated by law to remain compliant with safety standards and avoid legal consequences. Neglecting this could lead to serious penalties and potential risk to employees.
Digitization of MSDS simplifies the maintenance process by facilitating easy access, rapid updates, and precise tracking. Transitioning to digital not only increases efficiency but also minimizes error risks inherent in manual processes. Investment in a robust system supporting regular updates and maintenance is advised. MSDS upkeep commitment transcends legal requirements and is about safeguarding a safe working environment.
How to Access Your MSDS
Accessing Material Safety Data Sheets (MSDS) is facilitated through suppliers, manufacturer websites, or third-party databases.
- Supplier: Suppliers, post-purchase, provide the requisite MSDS for chemical products. Requesting them is encouraged.
- Manufacturer’s Website: MSDS are often accessible online via the manufacturers’ websites. Navigate to sections labeled ‘Safety Data Sheets’ or ‘Product Safety’ and locate the specific product.
- Third-Party Database: MSDS databases such as MSDSonline or Chemwatch offer extensive access to numerous MSDS.
Differences Between MSDS and SDS
Understanding the difference between Material Safety Data Sheets (MSDS) and Safety Data Sheets (SDS) is crucial. While MSDS, the older format, lacks standardization leading to inconsistent information and incomplete hazard details, SDS is an improved version overcoming these limitations. SDS provides a consistent 16-section format, supplying comprehensive details on chemical properties, hazards, protective measures, and emergency procedures. This evolution from MSDS to SDS has enhanced the communication of chemical safety data. Understanding these differences is essential for informed decision-making in chemical safety management.
Common Misconceptions About MSDS
MSDS misconceptions need debunking for proper understanding and usage.
- All substances need MSDS, not just hazardous ones: MSDS are essential for all substances used in labs or industrial settings, providing critical data on their handling, storage, and disposal.
- MSDS don’t contain complete substance information: MSDS offer extensive data but may omit certain specifics due to proprietary constraints or scientific knowledge limitations.
- MSDS vary by manufacturer and origin country: The layout, content, and detail level of the MSDS can differ based on its source, causing variation among MSDS.
Effective usage of MSDS, a key safety tool, requires thorough reading and comprehension. If in doubt, ask questions. Stay informed and safe.
MSDS for Non-Chemical Products
Non-chemical products necessitate Material Safety Data Sheets (MSDS) for compliance and safety in handling, use, and disposal. Interpreting these MSDS, understanding their importance, and knowing their specific details are crucial.
Understanding Non-Chemical MSDS
We’ll explore non-chemical Material Safety Data Sheets (MSDS), crucial for safety information, especially for items like biohazardous materials. However, understanding non-chemical MSDS requires acknowledging their limitations, including not covering all potential hazards, possibly lacking detailed information on long-term health effects, and potentially providing less extensive data compared to chemical MSDS.
Importance of MSDS Compliance
MSDS compliance is essential for a safe, legally compliant workplace. Understanding its legalities, though complex, is mandatory, not optional. The technicality of data sheets may pose compliance challenges, but they aim to safeguard against potential hazards. These sheets impart vital information on properties, hazards, handling, storage, and disposal of materials. Non-compliance risks severe consequences like fines, penalties, or business shutdown. It’s vital to effectively train staff on MSDS guidelines for proper implementation. Safety and compliance aren’t just legalities but sound business practice.
MSDS Contents and Interpretation
Compliance and understanding of Material Safety Data Sheets (MSDS) are crucial not only for hazardous chemicals but also for non-chemical products. MSDS provide vital data about product properties and hazards. However, ‘MSDS Limitations’ exist; these sheets typically exclude product effectiveness information and application guidance. ‘Legal Implications’ are critical, non-compliance can lead to substantial fines and legal complications. For efficient utilization:
- Thoroughly review the entire MSDS for complete information.
- Seek professional advice for interpretation or queries.
- Ensure updated MSDS are readily available for reference and inspections.
International Standards for MSDS
International standards for Material Safety Data Sheets (MSDS) aim to provide consistent, reliable information on hazardous substances globally. These standards, known as Global Harmonization, unify the classification and communication of chemical hazards. However, challenges exist due to varying hazard definitions across countries, causing potential confusion. MSDS, while a critical communication tool, doesn’t directly control or mitigate risks.
To address these limitations, the Globally Harmonized System of Classification and Labelling of Chemicals (GHS) was established. This system defines health, physical, and environmental hazards of chemicals to offer a uniform approach. It simplifies users’ understanding and handling of hazardous materials.
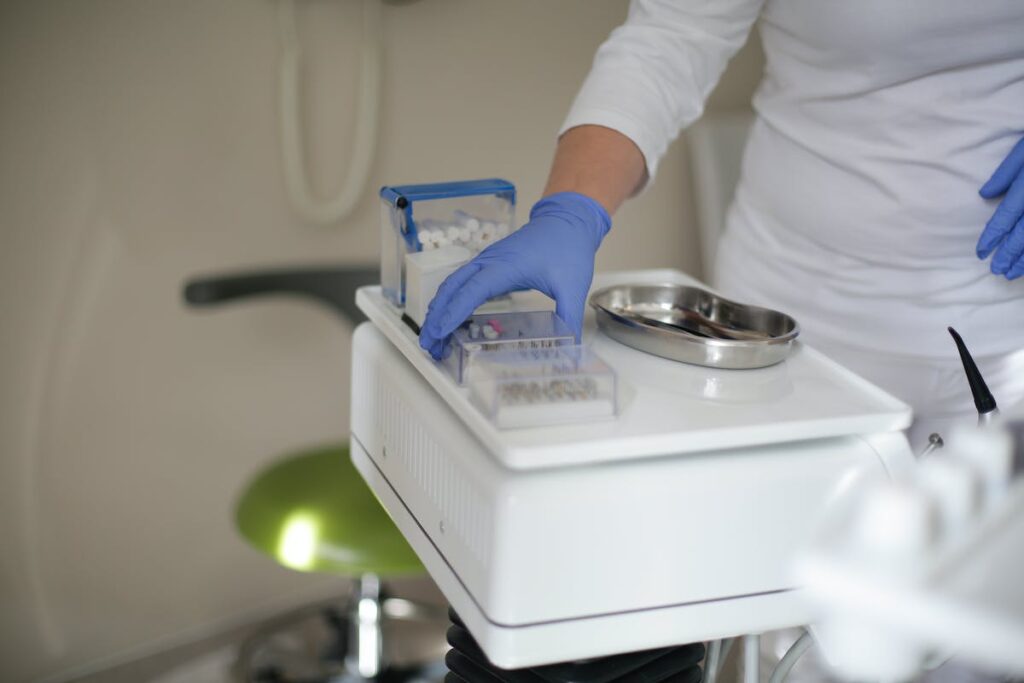
Case Study: MSDS Mishaps
Instances of MSDS misinterpretations and neglect often result in severe mishaps. The frequency of these consequences is higher than generally perceived. Highlighting the importance of accurate comprehension and implementation of these safety guidelines are certain case studies:
- Incorrect MSDS interpretation led a Texas chemical plant to wrongly store a volatile compound, triggering an explosion, causing extensive damage and fatalities.
- A pharmaceutical company’s MSDS oversight on a powerful drug exposed several lab workers to health risks.
- A manufacturing firm’s MSDS disregard resulted in hazardous waste improper disposal, inflicting significant environmental harm.
These cases underline the critical role of MSDS guidelines. They are not mere paper sheets but a lifeline for workers and the environment. Even minor oversights in understanding these safety sheets can yield disastrous results.
Tips for Effective MSDS Management
Effectively managing MSDS enhances safety performance. Comprehending MSDS importance involves understanding each section’s intricacies. This knowledge ensures workplace safety. Crucial MSDS procedures include establishing handling, storage, and disposal processes for hazardous materials.
Understanding MSDS Importance
Understanding the importance of Material Safety Data Sheets (MSDS) involves recognizing their role in workplace safety and regulatory compliance. Additionally, acknowledging their limitations and growth over time is essential.
- MSDS provide critical data on work environment materials and chemicals.
- They highlight potential risks, promote safe handling practices, and detail emergency responses.
- MSDS have limitations due to lack of specificity, leading to possible misinterpretations.
The evolution of MSDS has resulted in more comprehensive, user-friendly tools. However, effective use, regular updates, and staff education remain key to harnessing their full potential. This understanding is crucial to appreciate MSDS importance in workplace safety.
Implementing MSDS Procedures
Efficient MSDS procedure implementation demands a strategic approach. This includes not only regulatory compliance but also promoting workplace safety. The primary step is the adoption of MSDS digitization, converting physical MSDS into digital formats. This facilitates seamless access, updates procedures, and elevates safety standards.
Investment in interactive MSDS training is the subsequent step. It engages employees, enhances understanding, and encourages compliance. It’s not merely about data possession but also about its interpretation and application by the team.
Regular reviews and updates of MSDS procedures are necessary. With changing regulations and new substances entering the workplace, staying updated is vital. A proactive approach to MSDS management is essential for workplace safety.
Frequently Asked Questions
What Are the Penalties for Not Complying With MSDS Regulations?
Non-compliance with MSDS regulations results in significant fines, potential imprisonment, and reputation damage. Adhering to these regulations is crucial for business safety and legality.
How Often Should MSDS Training Be Conducted for Employees?
Conduct MSDS training annually, incorporating regulatory updates as needed. This ensures employee compliance, risk mitigation, and avoidance of penalties.
Can a Company Refuse to Provide MSDS for Their Products?
Company refusal to provide MSDS for products is not permissible. MSDS accessibility, product transparency, worker safety, and proper substance handling necessitate this legal obligation.
Are There Any Specific Software or Tools Available for Managing MSDS Documents?
Yes, specific software tools exist for MSDS document management. Such tools enable MSDS digitization, promoting efficiency. It is crucial to consider factors such as usability, functionality, and the provider’s industry knowledge during software selection.
How Can a Company Transition From MSDS to SDS, Considering the Differences Between the Two?
Transitioning from MSDS to SDS involves inventory updates, staff training on new formats, and potential investment in management software, despite facing implementation challenges and cost impacts.
Conclusion
Understanding and applying Material Safety Data Sheets (MSDS) is key for workplace safety. MSDS isn’t solely about chemical products, but crucial for a safe environment. Adherence to MSDS requirements and international standards aids in preventing mishaps. Effective MSDS management powerfully ensures safety, mitigates risks, and promotes a healthy work atmosphere. MSDS compliance isn’t just regulatory, it’s about care.